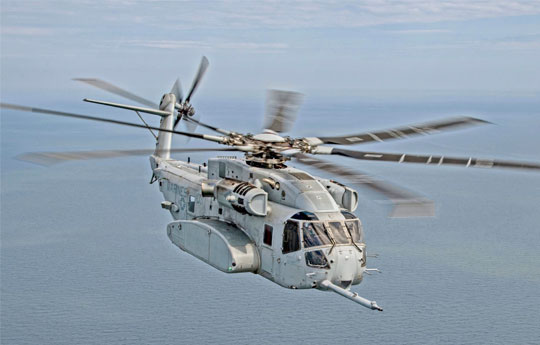
Aerospace Case Study
Sikorsky CH-53K King Stallion Parking Brake Assembly
Overview
Lockheed Martin, a global security and aerospace company, conducts the majority of its business with the U.S. Department of Defense and U.S. federal government agencies. Sikorsky, a Lockheed Martin Company, supplies military and rotary-wing aircraft to all five branches of the U.S. armed forces, in addition to providing military services and serving commercial operators in 40 nations.
Straton is a Lockheed Martin - Rotary and Mission Systems Elite Supplier and a Sikorsky Supplier of the Year winner.
Problem
Straton was contracted to build a prototype parking brake assembly because no other suppliers were willing to bid on the project, citing its complexity and specific development requirements.
The assembly consisted of multiple specialty materials, including Aluminum, Stainless Steel, Bearing Bronze, Titanium, and Nylon. It combined traditional and modern designs. Some components are legacy hand-drawn parts, while others are based on Model Based Drawings.
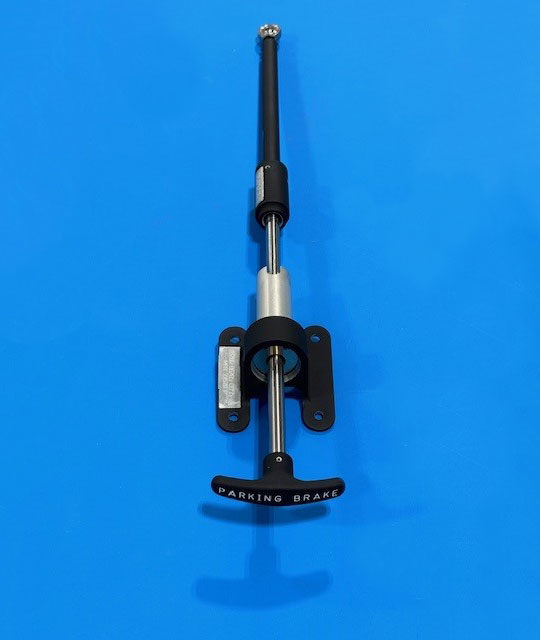
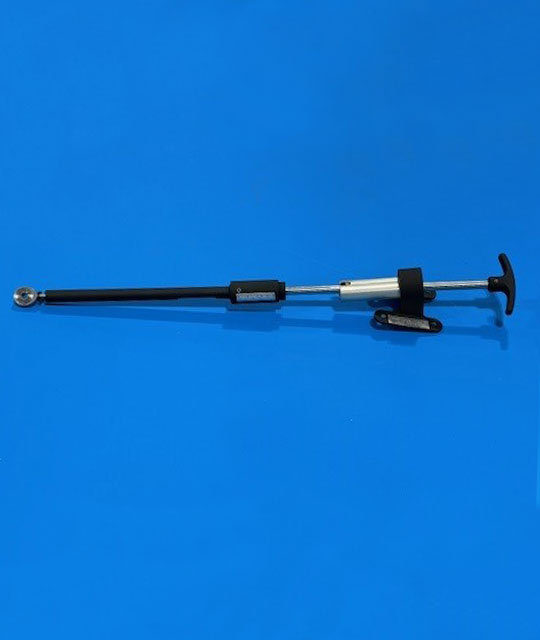
CH53K – Landing Gear Parking Brake Assembly
Solution
The customer tasked Straton with assessing the manufacturability of the hybrid design and identifying potential challenges or risks affecting component assembly. To achieve this, Straton’s engineering team analyzed various materials suitable for the unique design specifications. Additionally, process and design engineers collaborated closely with production floor personnel to pinpoint any areas where part geometry might hinder fit and functionality.
The assessment revealed potential challenges, such as issues with paint and sealant that could complicate assembly. Ultimately, the design analysis addressed these concerns by modifying certain aspects of the design and refining the manufacturing process. Consequently, this modification improved performance and reduced production costs.
Modifications included:
- The part models contained drafting errors that required correction.
- Specifications for materials and weight allowances required revisions during the manufacturing process.
- Simplified geometric tolerance schemes to lower costs.
Outcome
The project took a year to complete, yet it will be delivered within our quoted timeframe. Based on all the input gathered for this prototype, the part will serve as the foundation for production across the entire fleet of 250 aircraft.